Ending a six-month-long saga, Thomas Point Lighthouse has finally received the needle-in-a-haystack wooden beam needed for its restoration. But it didn’t come easy: getting the piece of wood to the Chesapeake Bay took a multi-state search.
As Bay Bulletin reported last month, the beloved Thomas Point lighthouse, a National Historic Site, is undergoing a big structural restoration project.
The unexpected need for the beam arose last spring when preservation foreman John Potvin and his team discovered the existing beam, made of not-so-tough Spanish cedar, had fully cracked under the weight of the privy that it supports.
Unable to simply buy a new beam at Home Depot or Lowe’s due to its size, or replace it with a modern steel beam due to historical preservation standards, Potvin consulted with the Maryland Historic Trust and began searching the East Coast for an old-world beam that would meet its requirements.
After a months-long search reaching from the Chesapeake Bay Maritime Museum to coastal Maine, Potvin had come up empty-handed. He enlisted the expertise of Glenn James, founder and president of CraftWright Timber Frame Company in Westminster, Maryland.
On a personal level, James jumped at the opportunity to help restore a lighthouse that he fondly recalled from childhood boat rides. More importantly, he saw the project as an unparalleled opportunity for a lifelong timber framer to “touch, reshape, learn from, and connect to, a centuries-old line of tradespeople through the most historically-significant structure on the Bay.”
So James visited the lighthouse, took every measurement imaginable, and began contacting his network of “wood dealers” in a search that he likens to Goldilocks searching for the perfect bowl of porridge – thus the nickname, “the Goldilocks beam.”
And after visiting six or seven beams that were either too young, too small, or too askew, James finally found his “just right” winner: a 30-foot, 2,000-pound piece of white oak salvaged from a long-gone barn in Northwestern Pennsylvania.
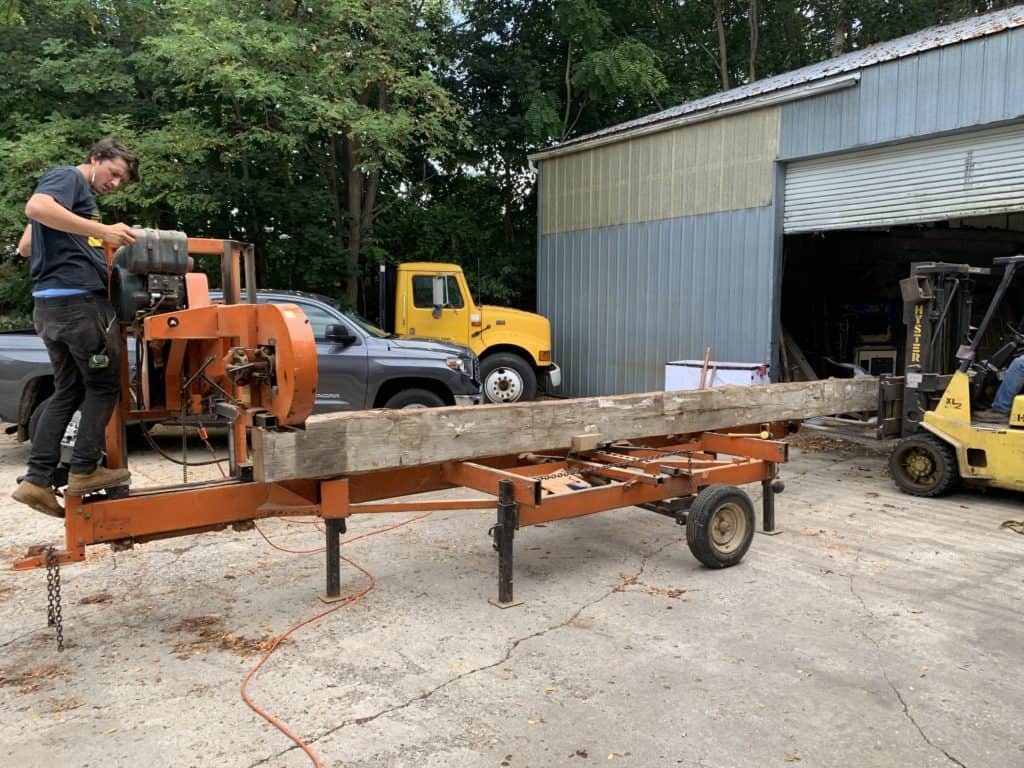
Following this “eureka” moment and a 77-mile flatbed drive from Gap, Pennyslvania to Westminster, James and the other members of the “Thomas Point beam team” (apprentice-employees Joseph, Connor, and Jeremy) sawmilled the tonner down to its final dimensions (4×12 inches), length (22 feet), and weight (roughly 375 pounds).
The team “dressed” her down with a salt preservative treatment, chiseled out 15 mortises (aka holes), and created (and donated to the project) eight replacement intersecting members, which connect the beam to the lighthouse’s steel superstructure.
Finally they painted the beam and members with two coats of oil-based primer and one coat of exterior acrylic donated by Fine Paints of Europe.
Then they loaded her up, trucked her the 61 miles from Craftwright to Potvin’s home on November 8, and carried her – “extremely carefully!,” notes Potvin, given the Chesapeake chop – to the lighthouse via workboat on November 11.
From there it was smooth sailing as the “beam team” installed the intersecting members, bolted Goldilocks in place, and replaced the decking that sits upon her.
Next up: A new privy, tie rods (a few of which, Potvin reports, were installed last week), and steel beams, all of which should be installed by 2022. But for now, Goldilocks marks a monumental end to 2019.
If you’d like to support the restoration, visit the Save the Thomas Point Lighthouse GoFundMe page, consider purchasing a Thomas Point Lighthouse Yeti Tumbler from Fawcett Boat Supplies, or visit USLHS.org in mid-December to purchase a Thomas Point Shoal Lighthouse 2020 calendar.
-Steve Adams